The Hand of the Artist
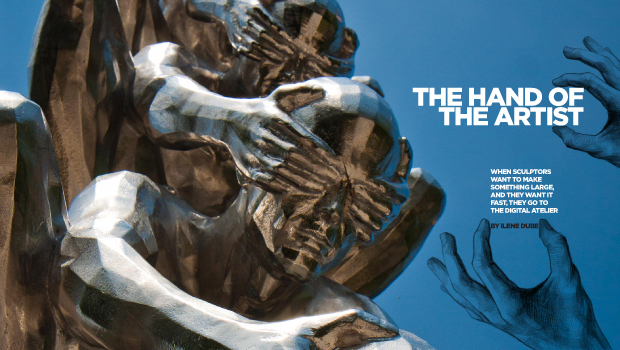
By Ilene Dube
When sculptors want to make something large, and they want it fast, they go to The Digital Atelier.
Last year, visitors lined up at the former Domino Sugar Factory in Williamsburg, Brooklyn, to view A Subtlety, Kara Walker’s homage to the African American slaves who built the sugar industry. Her giant white sphinx coated in 40 tons of sugar towered over its visitors at 75 feet tall. This was the first sculpture for the artist, a 1997 MacArthur Fellow previously known for two-dimensional silhouettes. The sphinx, with exaggerated African features, was accompanied by 15 “sugar babies” – molasses boys bearing baskets of bounty.
Under all that sugar were 330 enormous cubes of Styrofoam that had shipped on 18 wheelers from the Hamilton, N.J.-based Digital Atelier. The Digital Atelier is a state-of-the-art mold making facility. In space leased from the Johnson Atelier, the for-profit company uses laser scanning, CNC (computer numeric control) milling and coating technologies for artists, architects, museums and the entertainment industry. Walker’s slave children were molded in rubber, then cast in sugar that slowly melted – video records of the installation show a brown molasses dripping into puddles on the floor.
When A Subtlety closed, 240 of those Styrofoam blocks were shipped back to Hamilton to be recycled. And should Walker ever want to recreate A Subtlety, the master file can be used.
In addition to Walker, Digital Atelier clients include Do Ho Suh, Kiki Smith, Carole Feuerman, Gordon Gund and Jeff Koons.
For Walker’s project, the Atelier began by scanning her 12-inch model to make an eight-foot model. Laser scanners shoot the object and collect data to make a three-dimensional file. “Once we have the file we can manipulate it the way the artist asks,” says President/CEO Jon Lash. Although there are many hands on the project, the artist exerts final control. “It’s the latest greatest revolution,” says the salt-and-pepper-haired Lash, with all modesty.
The final work can be milled in materials from acrylic, nylon and wood to metal and plastic. Sculptor Matthew Day Jackson supplies the Atelier with the repurposed materials from which his work is to be milled. Using video cameras and computers, Jackson can watch the milling from his Brooklyn studio and direct the process.
“We don’t see people that often,” says Lash, sitting in a room with computers. “They come for the finishing. Most projects come in as small models or maquettes and we talk over the phone.”
The Atelier is currently bidding on a project for John Portman, the architect known for creating the Atlanta skyline. Lash zooms in on a detail to show how it’s made up of small triangles, what he calls a point cloud, or points in space. The software fills it in, he says, to create a polygonal model. He is assisted by John Rannou, an engineer, and Brad Warner, a programmer. “We hire people from art and engineering schools,” says Lash. “Princeton University and the University of Pennsylvania have combined art, architecture and engineering programs.”
Out on the milling floor, monitors surround the project to send data from the lab to the foundry. Lash’s son, Sawyer, is working in his father’s company while on break from the School of Visual Arts at Tucson, Arizona. With an interest in animation and three-dimensional manipulations, he is learning programs so, as his father says with a grin, he’ll have something to fall back on.
Architectural restoration projects have included crumbling facades. Stone walls for Longwood Gardens are being milled in foam so the committee can preview it and make decisions before its final execution in stone.
For Paramount, the Digital Atelier fabricated a David-like statue of Sacha Baron Cohen and backdrops for Men in Black. Other projects included work on Shrek and Miss Piggy for Henson Studios and fabricating cars for Disney. Also underway is a re-creation of the Porsche James Dean drove to his death in 1955. The fire melted all but the steel frame of the original, which is being restored in cherry with an aluminum body.
“Conservators come to us with projects,” says Lash, giving an example of a masthead for the Naval Academy. “Most museums are now scanning important pieces, so if they are damaged they can be restored digitally.”
Conservators for an underground mural in Nicaragua that was compromised by changes in humidity worked with the Digital Atelier to scan and reproduce it, preserving the original colors. After it travels, the reproduction will be installed outside the cave in Nicaragua.
“You know that David outside the Uffizi is not the real David,” says Lash. “The real David was attacked by chemicals in the air.” Lash gave a talk on digital sculpture at Florence’s museum. “Over the next 50 to 100 years they’re going to remake all the sculpture in the Milan Cathedral. The European Union is giving the money to train digital carvers. It preserves the apprentice program and starts a new business,” he says.
THE EYE OF THE ARTIST
Lash himself started as a sculptor and apprentice in the Johnson Atelier, where he met his wife, Dona Warner. She headed the metal finish department and became director. In his own work, Lash began as a figurative artist who eventually turned to abstraction. As an apprentice he worked with Georgia O’Keeffe on casting and enlarging her aluminum sculpture in the 1980s. He was promoted to staff, then worked in every department before becoming supervisor and director of special projects.
“I saw the sculpture world changing and went to Seward Johnson and told him about sculpting through digital means. Much of what was formerly done by hand and took months, if not years, is now possible to accomplish in weeks with fewer steps and less labor. He asked, what would I need to do that? He met with the board and they said ‘no way.’ A $100,000 grant was then received to develop a start-up within Johnson Atelier, from within Atlantic Foundation. This was in 1998, and no one else was doing this, says Lash – which meant learning by trial and error.
“By 2002, the Digital Atelier had taken off, and we went to the board and said we have a problem – we’re making money.” Making money can be problematic for a not-for-profit. “The IRS said it would allow the Sculpture Foundation to have a for-profit subsidiary for four years” but then it would have to be liquidated.
Johnson was supportive of the idea all along, says Lash. In 2011, the Digital Atelier was sold to Lash, who leases space from the Johnson Atelier.
Although he can’t talk much about it, Lash says he is working on a project with Koons that is of an experimental nature. Koons wants to make his piece out of an expensive stone. “To check the tool paths, he is doing it on a dense urethane first so the stone will not be ruined. We’re working closely with his studio.”
Digital Atelier made prototypes for the Jeff Koons studios of the Gorilla and other pieces in urethane and other foams before the final pieces were made by his studio in their final medium. “He likes to see the object first at full scale. He has his own computer modeling staff that can make changes before it goes into the final material.”
A FAMILY AFFAIR
The former Stone Division of the Johnson Atelier, which became the Digital Stone Project, was bought by Koons, who moved it to Morrisville, Pennsylvania, where it operates solely for his own use. Lash’s wife now works as a manager for Koons.
Jon and Dona keep a studio at home, but have little time for their own work. “This keeps me going 12 hours a day,” says Lash, who stays awake at night answering e-mails from Korea, Belgium and China in the wee hours. But it sates his artistic passions.
A customer calls to find out how much lead time is needed for a project. Lash asks his assistant to say three weeks. “People are looking for new materials, and they’re looking for a recommendation on what materials to use. I tell them if it won’t work in wood, or what changes they’d need to make to make it work in wood.
“They always control the project,” continues Lash. “You learn to use someone else’s hands. Jeff [Koons] says he doesn’t touch his own work but he’s a total control fanatic. He doesn’t take ‘no’ – someone in the world can do it the way he wants.”
Kiki Smith is more hands on. “She comes to do sanding and detail work,” reports Lash. “Tom Otterness likes to do everything. He does all the surface finishing. We make the armature, then the artist can put a fingerprint on it.
“The argument,” continues Lash, “is that sculpture will lose its heart if it is made by machine. But sculpture has always been made by machine.”